Zastosowanie Design of Experiment w systemie Autodesk Moldflow Insight – Biuletyn Moldflow 01/2018

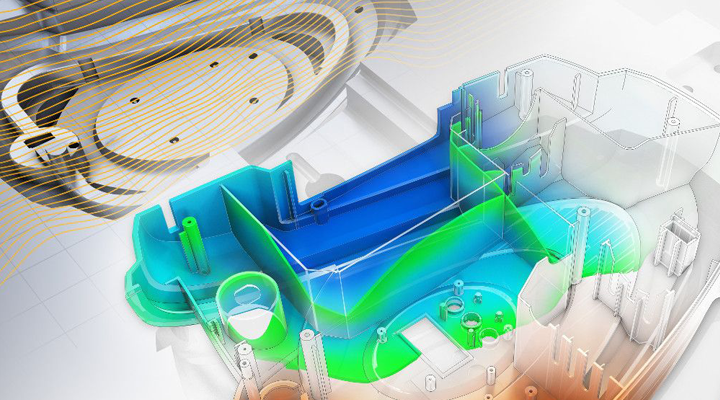
Zastosowanie Design of Experiment w systemie Autodesk Moldflow Insight (rozważania ogólne, prosty przykład oraz nowości w najnowszych wersjach systemu)
Chyba najbardziej przełomowymi rozszerzeniami funkcjonalności systemu Moldflow Insight, o jakie wzbogacony on został po przejęciu przez Autodesk są do tej pory bez wątpienia:
- Technologia Cool(FEM): nie tylko znacznie podnosząca precyzję samej analizy chłodzenia jako takiej, ale również umożliwiająca sukcesywne wprowadzanie kolejnych możliwości symulacyjnych zaawansowanych odmian technologii wtrysku, a wymagających dyskretyzacji bryły formy wtryskowej (i w wszystkich, niezbędnych jej części składowych – nie tylko rdzeni, wkładek i elementów gorąco-kanałowych, ale również grzałek, cewek indukcyjnych itp.) siatką elementów skończonych 3D.
- Zautomatyzowane metody optymalizacji, wspomagające analityka w projektowaniu kolejnych analiz w optymalizacyjnym łańcuch iteracyjnym:
a. Design of Experiment (DoE)
b. Parametric Study (sparametryzowane studium optymalizacyjne)
W niniejszym odcinku naszego biuletynu omówimy pokrótce Projektowanie Eksperymentu (DoE) – przybliżając czytelnikom (w tym początkującym, czy wręcz dopiero potencjalnym, użytkownikom systemu Moldflow) ogólne zasady, jak i najważniejsze szczegóły, posługiwania się tym zaawansowanym narzędziem. Nie będziemy zagłębiać się w skomplikowane, oparte na zaawansowanych metodach statycznych zasady działania algorytmów DoE (gdzie dodatkowo olbrzymią rolę odgrywa know-how w dziedzinie przetwórstwa wtryskowego tworzyw sztucznych, zgromadzone przez ponad 40 lat istnienia tego systemu). Najistotniejsze informacje z praktycznego punktu widzenia wspomnimy przy okazji omawiania 4 „trybów działania” DoE w Moldflow.
DoE Builder – czyli kiedy i dlaczego decydować się na przygotowanie i wykonanie DoE
Pracując nad niejednym studium – będącym, jak doskonale wiedzą użytkownicy systemu Moldflow – „szczególnym przypadkiem” projektu z modelem (zarówno CAD, jak i MES) wypraski i narzędzia, zestawem parametrów przetwórstwa i stosowanego materiału, sekwencją analiz oraz celów i kryteriów optymalizacyjnych (jakościowych), po poświęceniu wielu godzin pracy analityka i jego komputera dla wykonania wielu przebiegów tejże sekwencji analiz i interpretacji ich rezultatów – nawet najbardziej doświadczony analityk Moldflow może znaleźć się w sytuacji, w której:
wyczerpał on wszystkie pomysły na spełnienie/osiągnięcie kryteriów optymalizacyjnych (poprzez „ręczne” wprowadzanie zmian do studium przed kolejnymi, iteracyjnymi przebiegami sekwencji analiz) – a kryteria optymalizacyjne (jakościowe) wciąż nie zostały osiągnięte!
Na szczęście, w sukurs przychodzi wtedy właśnie narzędzie, będące tematem niniejszych rozważań: Design of Experiments, czyli DoE. Dostępne jest ono dla każdego rodzaju studium Moldflow – bez względu na stosowaną odmianę technologii wtrysku, użyty materiał (termoplastyczny bądź termoutwardzalny), wyznaczone cele optymalizacyjne (czy innymi słowy – kryteria jakościowe), oraz zależną od tych celów, stosowaną sekwencję analiz. Jego zastosowanie pozwala – mówiąc najkrócej i najprościej – wykorzystać system Moldflow Insight do:
- modyfikacji wybranego zestawu tzw. „zmiennych wpływu” (influence variables – w dalszej części zwane po prostu „parametrami”), na podstawie interpretacji aktualnych rezultatów
- automatycznego przygotowania i wykonania odpowiedniej liczby właściwej sekwencji analiz
- na podstawie wyników wszystkich tych analiz, wyznaczenia takich wartości zmiennych wpływu, przy których założone podczas przygotowania DoE kryteria jakości (Quality Criteria) będą spełnione (tj. zbliżoną w najwyższym, możliwym stopniu i z uwzględnieniem względnego znaczenia każdego z tych kryteriów wobec pozostałych (określnego przypisaną doń wagą – liczbą z przedziału [1,10])
Aby przygotować i wykonać DoE i znaleźć optymalne wartości zmiennych wpływu z jego pomocą, uruchamiamy „wizard” zwany „Doe Builder”. Poniżej – w oparciu o poszczególne ekrany wizarda – nakreślono proces przygotowania eksperymentu dla prostego, testowego studium, w którym problemem jest wtryśnięcie prostej wypraski w kształcie kubka (wtrysk centralny w denko; chłodzenie stempla – mocno rozbudowane dla osiągnięcia minimalnego czasu cyklu w masowej produkcji) – tak, aby spełnić kryteria jakości dotyczące jego kształtu (minimalizacja odkształceń – a w szczególności zachowanie płaskości denka oraz okrągłości krawędzi). Każdy „przebieg” w ramach budowanego eksperymentu oznacza wykonanie pełnej sekwencji analiz Cool(FEM) + Flow +Warp.
1. Wybór trybu eksperymentu (1-szy ekran wizarda DoE Builder)
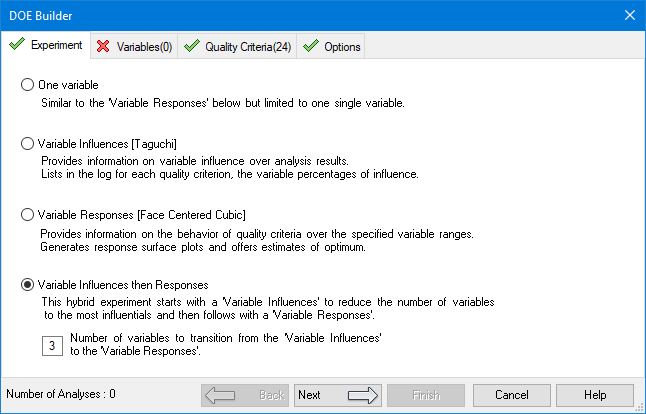
Design of Experiment może przebiegać w jednym z czterech trybów, wybranym na pierwszym ekranie wizarda DoE:
- One variable – wyznaczanie odpowiedzi układu na zmianę wartości pojedynczej zmiennej wpływu. System znajduje taką jej wartość, przy której kryteria jakości (zdefiniowane dalej) najbliższe są wartościom optymalnym
- Variable Influences (Taguchi) – analiza przesiewowa wg metody Taguchiego; spośród wszystkich zmiennych wpływu, wskazanych przez użytkownika (na kolejnym ekranie wizarda) – system wyznacza parametry, mające największy wpływ na kryteria jakości – po czym szereguje te zmienne wg (wyrażonej procentowo) wielkości ich wpływu ma poszczególne kryteria jakości
- Variable Responses (Face Centered Cubic) – system znajduje odpowiedzi układu na zadaną przez użytkownika zmienność wybranych przez niego parametrów; tryb ten stosuje się wtedy, gdy wiadomo które z nich maja największy wpływ na kryteria jakości. DoE znajduje optymalne wartości zmiennych wpływu, zapewniające spełnienie wszystkich zdefiniowanych kryteriów jakościowych, biorąc przy tym pod uwagę przypisaną każdemu z nich wagę
- Variable Influences then Responses – gdy użytkownik nie wie, które parametry mają największy wpływ na wybrane kryteria jakości, DoE może wykonać za użytkownika podwójną pracę: najpierw spośród wskazanej liczby zmiennych wpływu, za pomocą analizy przesiewowej Taguchiego, system wyłania i porządkuje (wg procentowej wielkości wpływu) najbardziej znaczące parametry. Następnie – dla pierwszych N zmiennych wpływu (wartość N określa liczba w polu na dole okna) – DoE znajduje odpowiedź układu, wyliczając takie wartości owych parametrów, dla których wybrane kryteria jakości najbliższe są wartościom optymalnym
Należy podkreślić, że liczba niezbędnych sekwencji analiz zależy oczywiście od liczby rozpatrywanych zmiennych wpływu ; dla Trybu nr 3 wynosi ona n^2+2n+1 (gdzie n to liczba rozpatrywanych parametrów). Gdy jednak zażądamy od systemu i analizy przesiewowej Taguchiego, i wyznaczenia odpowiedzi (Tryb nr 4) – liczba ta ulega podwojeniu! Przystępując do analizy DoE dysponować więc musimy odpowiednią mocą obliczeniową oraz wystarczającą ilością czasu; najbardziej efektywnie pracuje DoE w Trybie nr 3 (tylko odpowiedzi) – dlatego dobrze jest, gdy doświadczenie użytkownika jest wystarczające dla samodzielnego wskazania najbardziej istotnych zmiennych wpływu, i ograniczenia DoE wyłącznie do znajdywania odpowiedzi układu i optymalnych wartości parametrów (zmiennych wpływu).
W przytaczanym tu prostym przykładzie optymalizacji kształtu kubka zdecydowano się właśnie na Tryb nr 3, a badanymi zmiennymi wpływu uczyniono – co widać poniżej na kolejnej stronie wizarda – parametry fazy docisku (czas jej trwania i wartość ciśnienia docisku, wyrażona w procentach maksymalnego ciśnienia wtrysku), oraz parametry chłodzenia (ciśnienie pompy tłoczącej chłodziwo oraz temperatura chłodziwa na wlocie układu chłodzenia stempla).
2. Wybór zmiennych wpływu (2-gi ekran wizarda DoE Builder)
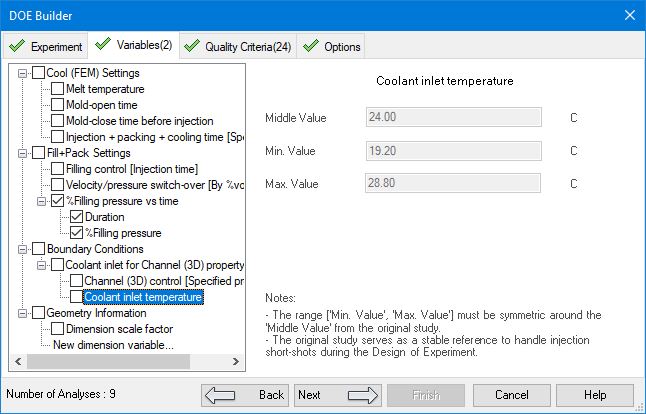
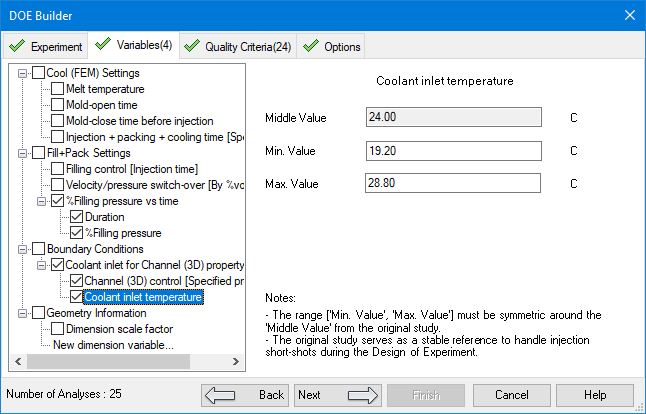
Na drugiej stronie wizarda „DoE Builder” wybieramy te spośród dostępnych zmiennych wpływu, na których zmienność odpowiedź układu chcemy badać i których optymalne (z punktu widzenia zdefiniowanej na kolejnej stronie kryteriów jakości) chcemy wyznaczyć poprzez przeprowadzenie DoE Typu 3. W lewym panelu zaznaczane są interesujące nas zmienne – prawy panel wyświetla wtedy ich aktualną wartość (taką, jaką mają w analizie, której wyniki są punktem wyjścia dla przygotowywanej analizy DoE – Middle Value) . Wartość ta pomniejszana i powiększona jest o tę samą wartość, zwaną „deltą”, i wszystkie 3 wartości danej zmiennej badane są w kolejnych sekwencjach analiz. Wartość owej „delty” proponowana jest przez system, ale użytkownik może ją edytować (np. zwiększyć, w celu rozszerzenia „pola poszukiwań”). Tak zdefiniowane zakresy zmienności zmiennych wpływu tworzą wielowymiarową przestrzeń (hiper-prostopadłościan; ma z nim związek nazwa metody – „Face Centered Cubic”), w ramach której wyliczana jest odpowiedź układu. Wyniki pracy DoE (odpowiedzi układu) przedstawiane są często jako tzw. response surfaces – przy czym (ze względu na ograniczenie możliwości wizualizacyjnych do 3 wymiarów) dana odpowiedź (kryterium jakości) wyświetlana jest jako funkcja co najwyżej 2 zmiennych wpływu (wykres 3D). Oczywiście – jeżeli do eksperymentu wybrano więcej, niż 2 zmienne wpływu – użytkownik może zmieniać dziedziny, reprezentowane osiami X oraz Y takiego wykresu, i prześledzić w ten sposób wszystkie response surfaces dla wybranego kryterium (wartość odpowiedzi, czyli jednego z kryteriów jakości, zawsze odczytywana jest na osi Z takiego wykresu).
2a. Co może być zmienną wpływu w Design of Experiments?
Warto w tym miejscu wyjaśnić, jakie wielkości i parametry mogą być zmiennymi wpływu. Od początku dostępności Design of Experiment w systemie Moldflow Insight są nimi praktycznie wszystkie parametry procesów – nie tylko dla tradycyjnego wtrysku tworzyw termoplastycznych lub termoutwardzalnych, ale również większości zaawansowanych odmian tego procesu. Przy czym przez „parametry procesu” rozumiemy nie tylko wszystkie wielkości technologiczne fazy wypełniania (jak szybkość wtrysku, temperatury tworzywa i formy, punkt przełączania V/P czy profil docisku) – ale również te, charakteryzujące chłodzenie formy (jak intensywność tłoczenia chłodziwa wyrażona ciśnieniem lub wydatkiem pompy, czy też temperatury chłodziwa na wlotach wszystkich segmentów układu chłodzenia formy). Parametrami dla DoE mogą być także zmienne wpływu, charakterystyczne dla danej odmiany procesu przetwórstwa (np. czas sieciowania w technologiach związanych z duroplastami, albo czas zwłoki przy wtrysku wspomaganym gazem) – a z drugiej strony parametry, charakteryzujące proces jako całość (np. czas cyklu).
Odmienną grupę zmiennych wpływu dla DoE stanowią parametry związane z geometrią. Do niedawna ich zastosowanie było raczej ograniczone – wynikało to z faktu, że geometria CAD nie mogła być modyfikowana w Synergy po zaimportowaniu modelu, wszelkie więc modyfikacje ograniczały się do działań na gotowej siatce MES. Dodatkowym ograniczeniem jest fakt, że system może manipulować grubością ścianki (czy innego elementu jak żeberko lub kominek) tylko w przypadku siatki DD albo MP; dla siatki 3D jest to niemożliwe.
Najnowsze wersje systemu Autodesk Moldflow Insight wnoszą znaczne poszerzenie możliwości w tym zakresie dzięki sukcesywnemu wprowadzaniu w ostatnich wydaniach systemu możliwości bezpośredniej modyfikacji geometrii CAD już po zaimportowaniu modelu. Istnieje możliwość nie tylko podstawowych operacji typu zmiana grubości (ścianki, żeberka,..) – ale wręcz przemieszczenia takich elementów względem pozostałej części modelu, a nawet ich dodawania albo usuwania.
Ten postęp umożliwił zapamiętywanie operacji na geometrii w listach modyfikacji, i manipulowanie modyfikacjami jako zmiennymi wpływu. Jeżeli chcemy zbadać wpływ zmiany grubości czy dokładnego położenia np. żeberka na odpowiedź układu, możemy to obecnie robić dla dowolnej z używanych technologii MES: system bowiem najpierw zaaplikuje zdefiniowaną zmianę bezpośrednio na geometrii modelu, a dopiero potem wygeneruje na tak zmodyfikowanej geometrii CAD siatkę MES.
3. 3. Wybór kryteriów jakości dla DoE (3-ci ekran wizarda DoE Builder)
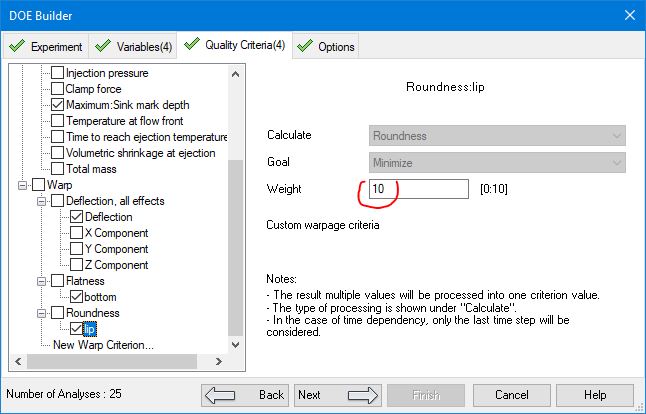
Lewy panel 3-go ekranu wizarda DoE Builder zawiera wszystkie rezultaty analiz, składających się na badaną sekwencję; są więc tu najważniejsze wyniki analiz: Flow (czyli FIll+Pack), Cool (FEM) oraz Warp. Można oczywiście zaznaczyć wszystkie – ale dla zwiększenia przejrzystości wyników użytkownik zwykle ogranicza się do tych najważniejszych, stanowiących kryteria jakości unikalne dla badanego studium. Ponadto – jeżeli studium zostało odpowiednio przygotowane przed uruchomieniem wizarda – mamy możliwość wyboru geometrycznych kryteriów jakości, związanych z wynikowym skurczem i ugięciem wypraski. Ponieważ w tym zakresie najnowsza wersja systemu Moldflow Insight (2018.2) przyniosła istotne nowości, omówimy te kryteria nieco bardziej szczegółowo
3a. Geometryczne kryteria jakości
Już na etapie konstrukcji wypraski powinno się zdecydować, które wymiary powinny bezwzględnie zmieścić się w zadanej tolerancji – mimo skurczu i odkształcenia, których w wyrobach formowanych wtryskowo z tworzyw termoplastycznych uniknąć nie sposób. Jeżeli np. wypraska stanowi część korpusu większego wyrobu i będzie skręcana z inną jego częścią – wzajemna odległość kominków pod śruby łączące winna być takim właśnie, dość ciasno tolerowanym wymiarem. Podczas pre-processingu (przygotowania studium do analizy w Synergy – środowisku GUI systemu Moldflow Insight), każdy taki wymiar krytyczny (Critical Dimension) między dwoma węzłami siatki MES definiuje się jako warunek brzegowy (Boundary Condition) zagadnienia (Menu->Optimization->Critical Dimensions). Każdy wymiar krytyczny zapamiętywany jest dla danego studium pod unikalną nazwą, która pojawi się jako jedno z geometrycznych kryteriów jakości w lewym panelu 3-ciej strony wizarda DoE Builder – i może zostać wybrana jako jedno z interesujących nas kryteriów jakości. Od wersji 2018.2 systemu, w tym samym Menu zdefiniować można jeszcze dwa rodzaje warunków brzegowych:
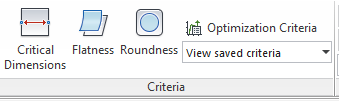
Płaskość (flatness) – wskazanie węzła na powierzchni, której płaskość jest krytyczna z punktu widzenia funkcjonalności lub estetyki wypraski, powala automatycznie stworzyć zbiór wszystkich węzłów na tej samek powierzchni. Po nadaniu mu unikalnej nazwy można taki zbiór węzłów zapamiętać w ramach studium, a podczas wyboru kryteriów jakościowych pojawi się on w lewym panelu 3-go okna wizardu DoE Builder. Należy pamiętać, że tak pojęta „płaskość” nie określa przesunięcia węzłów względem oryginalnej geometrii; jest to po prostu odległość płaszczyzn, wyznaczonych wybranymi węzłami (na zasadzie best fit), przed i po skurczu/odkształceniu.
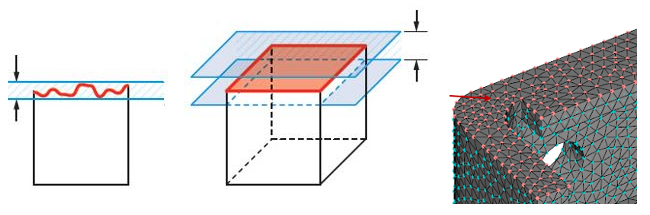
Okrągłość (roundness) – kolejny warunek brzegowy, pozwalający zdefiniować kryterium jakościowe dla Design of Experiments. Rozumie się pod tym pojęciem maksymalne, całkowite odchylenie powtryskowego położenia definiujących ją węzłów, od okręgu typu „best fit”. Jest to więc suma największych dodatnich jak i ujemnych przesunięć węzłów od położenia, wynikającego z promienia okręgu przed skurczem/odkształceniem. Tak pojęte kryterium typu roundness nie musi więc (choć może) dotyczyć konkretnych cech geometrii w konkretnym układzie współrzędnych – węzły można wybrać arbitralnie.
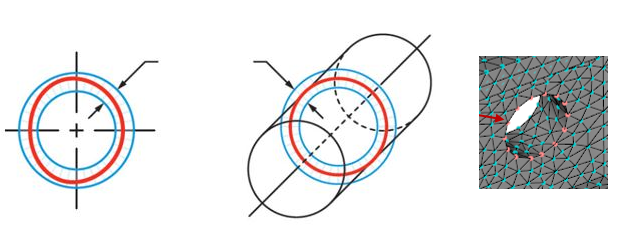
W przypadku naszego (celowo skrajnie uproszczonego na potrzeby niniejszych rozważań na temat DoE) studium, jako kryteria jakości wybrano rezultat „Sink Mark Depth” (głębokość zapadnięć, powstałych w wyniku niedostatecznego dopakowania gniazda w fazie docisku) – a także poszczególne składowe odkształceń, wyliczone w analizie Warp. Oceniając mocno zdeformowany kształt krawędzi oraz denka testowego kubka zdecydowano, aby zdefiniować w opisany powyżej sposób kryterium okrągłości dla węzłów na tej krawędzi (warunek brzegowy zapisany został pod nazwą „lip”), jak również kryterium płaskości dla węzłów na powierzchni dna kubka (warunek brzegowy „bottom”). Na poniższych widokach modelu w Synergy węzły, definiujące oba te warunki brzegowe, wyświetlane są w ciemno-niebieskim kolorze:
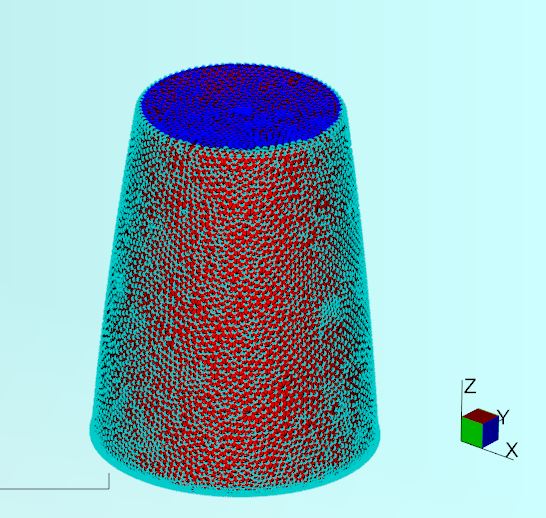
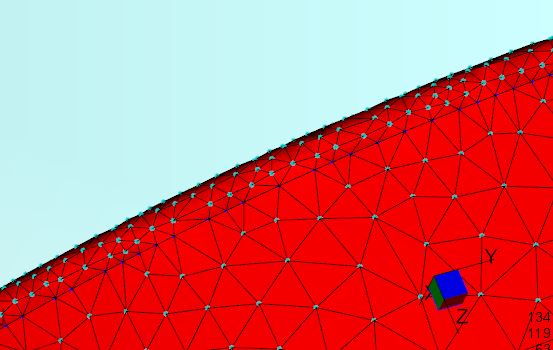
Poszczególnym kryteriom jakości, wybranym na 3-im ekranie DoE Buildera dla naszego bardzo prostego modelu, ilustrującego proces przygotowania Design of Experimets oraz jego rezultaty, przypisano następujące wagi:
- Sink Mark Depth – waga: 1
- Deflection – waga: 2
- Flatness „Bottom” – waga: 5
- Roundness „lip” – waga: 10
Przypomnijmy w tym miejscu, że nadanie tak wysokiej wagi ostatniemu z powyższych kryteriów jakości podyktowane było faktem, iż ocena rezultatów analizy poprzedzającej przygotowanie DoE wykazała odstępstwa od okrągłego kształtu krawędzi kubka tak duże, iż – gdyby nie udało się ich zredukować – jakość wypraski byłaby nie do przyjęcia (Rys. 7).
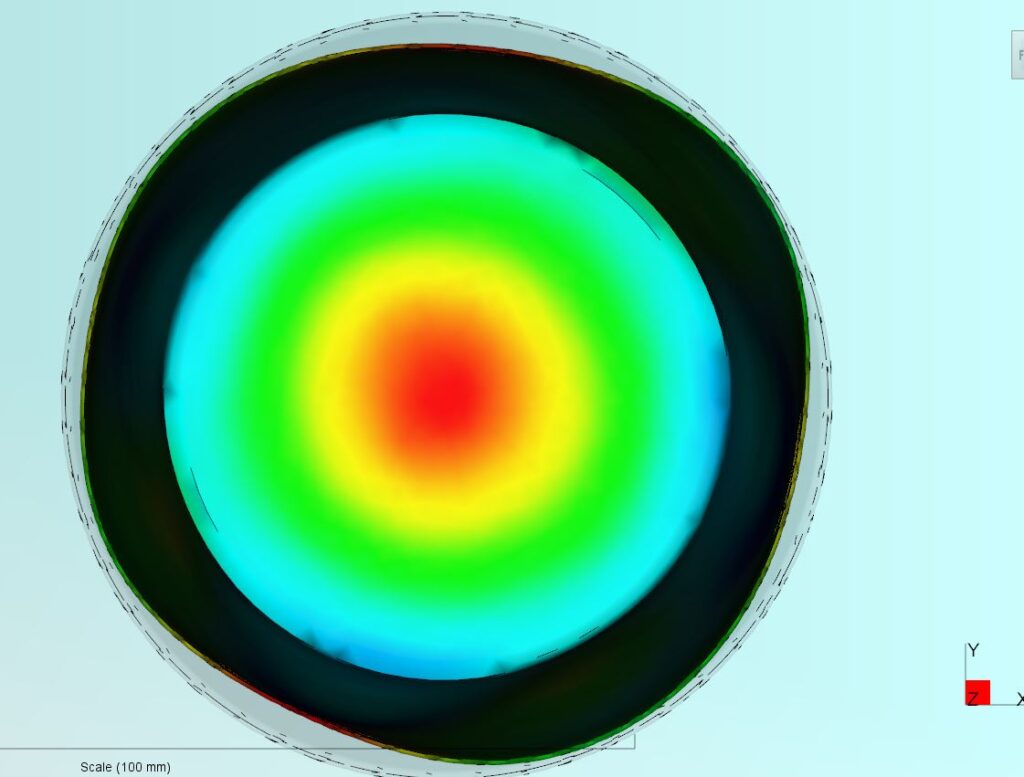
4. Opcjonalne ustawienia DoE
W ostatnim oknie wizarda DoE Builder użytkownik dokonuje wyboru kilku opcji; są to:
- Keep Result Files – gdy opcja jest włączona, wszystkie sekwencje analiz wykonane przez DoE pozostają na dysku komputera (poniżej opisano scenariusz, w którym jest to przydatne; pamiętać jednak należy o odpowiednio dużej, wolnej przestrzeni dyskowej przed uruchomieniem DoE z niniejszą opcją włączoną)
- Save results in CSV file – domyślnie włączona opcja pozwalająca przeglądać wyniki doE w arkuszu Excel
- Maximum number of relaunch – określona przez użytkownika liczba prób powtórzenia analizy, która – np. z powodu zbyt małej wartości temperatury tworzywa (gdy jest ona jednym z parametrów DoE) – zakończyła się niedotryskiem (Short shot). Przed każdą kolejna próbą, system odpowiednio zmniejszy deltę tej zmiennej wpływu, efektywnie podnosząc minimalną wartość temperatury tworzywa – co powinno pomóc uniknąć tego błędu.
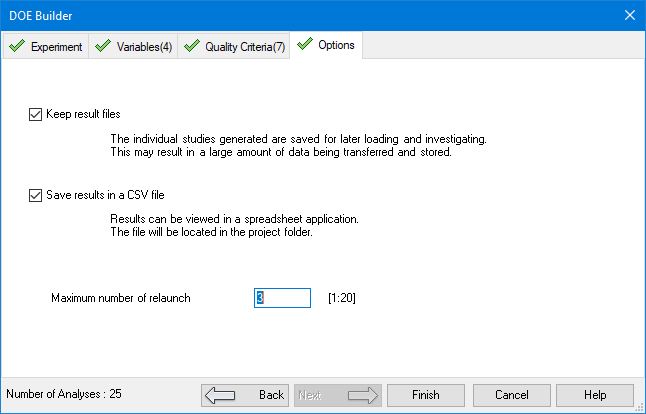
5. Przebieg i rezultaty analizy DoE
Już podczas trwania obliczeń, w logu analizy DoE pojawiają się interesujące informacje – np. wyświetlona jest liczba sekwencji analiz: zakończonych błędem, oczekujących, wykonywanych i zakończonych. Po ukończeniu wszystkich analiz, w podsumowaniu eksperymentu wyświetlana jest osiągnięta wartość optymalna każdego kryterium jakości wraz z wartościami zmiennych wpływu, dla których to optimum zostało osiągnięte. Np. dla kryterium Roudness: lip w naszym prostym modelu testowym:
Optimum on quality #4, Roundness:lip
Calculate = Out-of-Roundness
Range = [ 0.0127036 : 0.0295999 ] mm
Minimum value = 0.0127036 mm
with 4.2 Bar as Channel (3D) control [Specified pressure]
with 32 C as Coolant inlet temperature
with -1 as Duration
with -0.2 as %Filling pressure
Podsumowanie wszystkich wykonanych w ramach eksperymentu sekwencji analiz jest dostępne w rezultacie pod nazwą „DoE Results Comparison Explorer”; po nałożeniu na tę tabelę filtra (ukrywającego wszystkie przebiegi, dla których to najbardziej nas interesujące kryterium miało wartość inną, niż optymalna – tabela wyświetla już tylko jedną sekwencje analiz z optymalnymi wartościami zmiennych wpływu (Rys. 9):
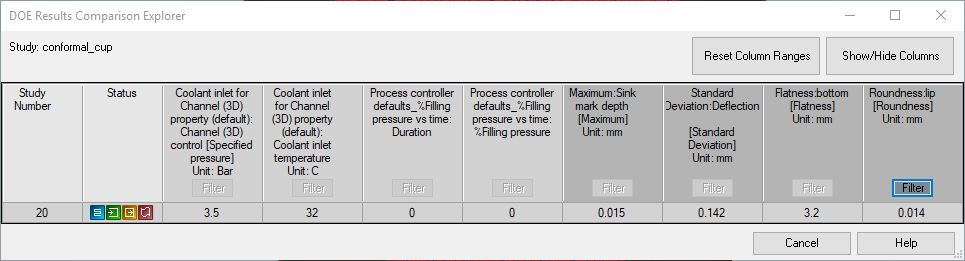
Poniżej wykres jednego z rezultatów wspomnianego wcześniej typu „DoE Response Surface” – wyświetlony dla tego samego kryterium jakości (Roundness: lip); wartość kryterium pokazana jest na osi Z. Domeny X oraz Y wybrać można z dwóch rozwijalnych list w oknie dialogowym, zaś wpływ pozostałych 2 zmiennych wpływu (czas trwania i ciśnienie fazy docisku) zmieniać można dostępnymi w tym oknie suwakami. Pozwala to nie tylko potwierdzić, że minimum odchylenia od okrągłości krawędzi kubka osiągana jest przy wartościach zmiennych wpływu, podanych w logu analizy DoE i potwierdzonych w eksploratorze wyników – ale również zbadać wrażliwość tego kryterium jakości na zmiany wszystkich parametrów.
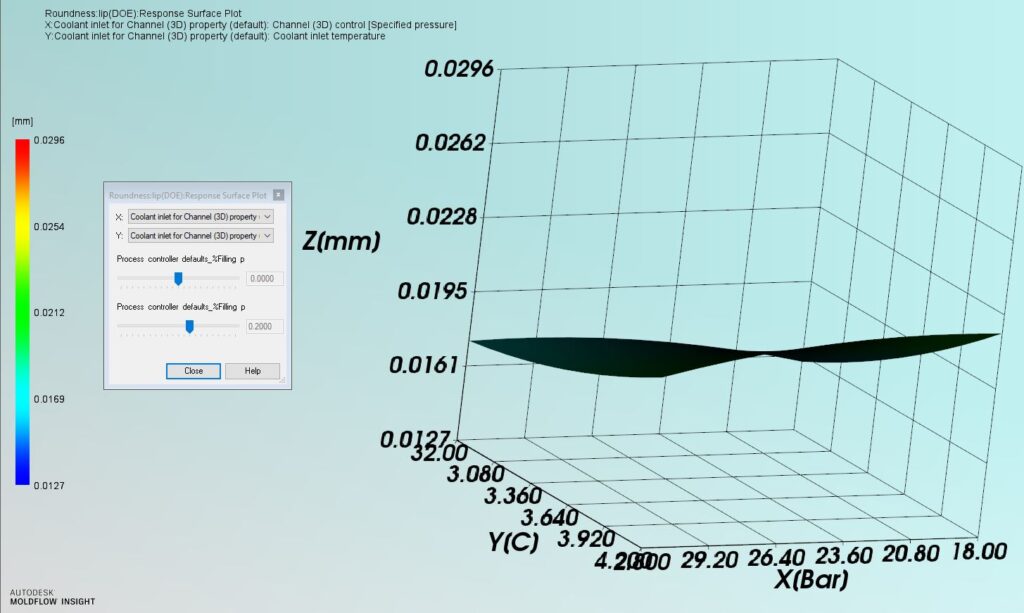
Natomiast bezsprzecznie najbardziej przekonujące jest porównanie silnie odkształconej krawędzi kubka (Rys. 7) z tym samym rezultatem analizy, wykonanej przy optymalnych wartościach wszystkich zmiennych wpływu:
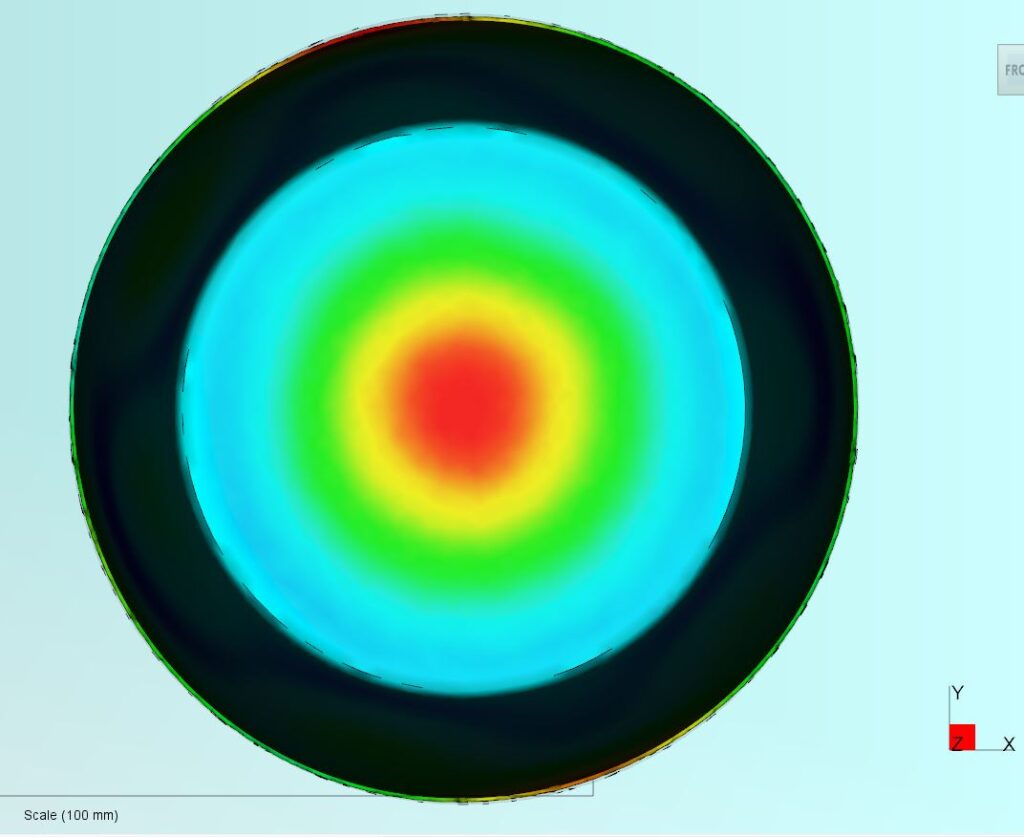
Opracował:
Piotr Woźniacki
Inżynier CAE/Moldflow
PROCAD SA